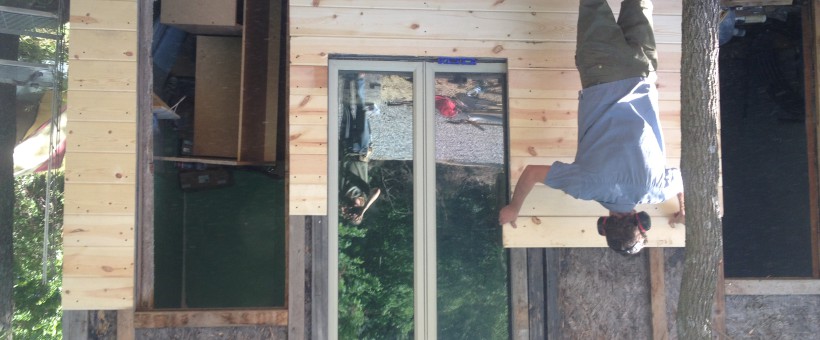
Days 11-12
Interns have been working around the clock to perfect 3D-prints and complete other tasks. While not all projects have been successful, they have gotten much closer to finishing most of what they set out to do this week.
Founding Director Marcin Jakubowski finished reviewing individual CEB Press modules Wednesday morning. A few modules are finished, but most at least require some polishing still.
Thursday’s morning meeting consisted of reviewing the progress from Wednesday on 3D-printers, pool assembly and the gazebo, along with issues people had with each project.
Additionally, they discussed how we can resolve remaining issues with the CNC Torch Table, particularly how it leaves a bunch of slag on the back of the metal even when the cuts are clean on top.
After both meetings, the interns continued finishing up modules as Marcin walked around helping the interns one-on-one.
At the Hab Lab
Once each 3D-printer finally started working, Emily Dixon, Gabriel Elkind, Greg Buckland, Juan Bennazar, Stephen Whiting and Moriah Baltz spent Wednesday and Thursday improving the quality of 3D-prints.
Emily, Greg, Juan and Moriah each have one printer they’re working to improve. Gabriel is adjusting the program that sends commands from individual computers to the printers.
“Each printer has its own failures,” Emily said, elaborating on the unique problems they had with each. One of the printers lacks a heated bed, while the prints on another flatten out a bit before hardening.
Thursday they managed to print more scaled-down CEB Press parts, but are still having problems with the height and quality of each print.
Outside/at the workshop
Graham Coffman, Jeff Adams, Guillaume Coudray and Brenna Fitzpatrick began constructing the gazebo, only to find that the materials they had to work with weren’t enough to build a structurally sound roof. Construction has temporarily come to a halt as interns brainstorm roofing alternatives.
On Thursday, Jeff led the installation of side panelling on one of the Solar Cabins with help from Steven, Juan and Sam Turner. Sam also planted several trees outside of Factor e Farm‘s MicroHouse.
Gillaume and Brenna cut the rest of plywood for the exterior soffits on the Hab Lab.
Clair Sprenger coordinated the pool assembly effort both days with help from Sam, Gabriel, Moriah, Graham, Jeff, Brenna, Juan, Stephen and Gullaume. After lots of confusion regarding the instructions, they managed to almost finish assembling the bottom framework.
Anthony Douglas continued working glitches with the CNC Torch Table with help from Sam, Gabriel and Steven. Right now they are trying to level the Torch Table and smooth out communication issues between the program controlling it and the machine itself.
Is the photo on the previous screen upside down?
I tried to make a comment about the torch table, but it did not go in. The “Leave a Comment” option needs to show the contents for each of the text entry boxes so people will know what goes where.
Torch Table. It seems that some part of the metal is melting rather than vaporizing. Things to try: 1. Increase the heat so the metal vaporizes before it can melt. 2. Make a partial cut, let it cool, then retrace to finish the cut after metal surrounding the cut has cooled, i.e. make two passes. I would cut mostly through because any slag will pool at the bottom, then be vaporized on the second pass. My thinking is that the surrounding metal becomes a heat sink pre-melting metal at the bottom of the cut. 3. Support the metal from below. Use plywood, tempered masonite, sheet rock alone. Or cover the support with metal to draw out some heat. The idea is that slag would have nowhere to run and pool if the cut is supported from the bottom. The supporting material(s) would likely be sacrificed in the cut. Watching the sparks from the cutting video I wondered if it is necessary to leave the cut open at the bottom for the material from the cut to flow out.
I would use tin or galvanized sheet metal on top of the supporting material. It would be thin metal.
What media are you referring to? I noticed that the video linked in the article above is from torch table prototype 1 which was years ago.
3 D Printing. Spool tension will also change as the spool is used because there will be less weight from the material. Try putting a mechanism to continuously or periodically turn the reel so plastic line is always hanging loosely. The printer won’t need to pull the line to get it to feed. It will always be available at the same (little or no) resistance regardless of the weight on the spool or how tightly it was wound. This could easily be tested simply by having someone unroll enough line as the 3D printer is working so that it never has to pull to get it.
Time stamp. My entries were made around 9:00 am Central Standard Time. I notice that the time shown is around 2:00 pm. Is this being hosted in a European time zone?
Width of cut – Torch table. A thinner (narrower) cut might generate less material to flow as slag from the opening at the bottom.